A seamer that is perfectly tailored to the Krones can filler
Filler and seamer from one manufacturer – it goes without saying that this set-up only offers advantages both for the production as well as for the operators. This exactly is the reason why Krones placed its Modulseam can seamer on the market in 2017. In the meantime, the machine has proven itself in the field and is consequently also part of the Modulfill Bloc FS-C for cans.
At a glance
- Perfect seamer for Modulfill can filler
- Output: up to 135,000 cans per hour
- Comprehensive cleaning concept
- Included as standard:
- Bubble breaker
- Under-lid gassing with CO2
- Quick-change handling parts
- Continuous servo drive concept
- Central lubrication unit
- Quickly adjustable quick-set cam for a swift change-over from steel to aluminium cans
Facts and figures
Application: Beverages
Capping heads | 6 | 8 |
12 |
14 | 18 |
Maximum output* (cans per minute) |
750 | 1,000 | 1,600 | 1,750 | 2,250 |
Adjustment range for can height (mm) |
88 – 205 | 88 – 205 | 88 – 205 | 88 – 205 | 88 – 205 |
Can diameter (mm) | 53 – 84 | 53 – 73 | 53 – 73** | 53 – 73** | 53 – 73** |
*Depending on the can format
**Depending on the filler pitch
Accessible from all sides
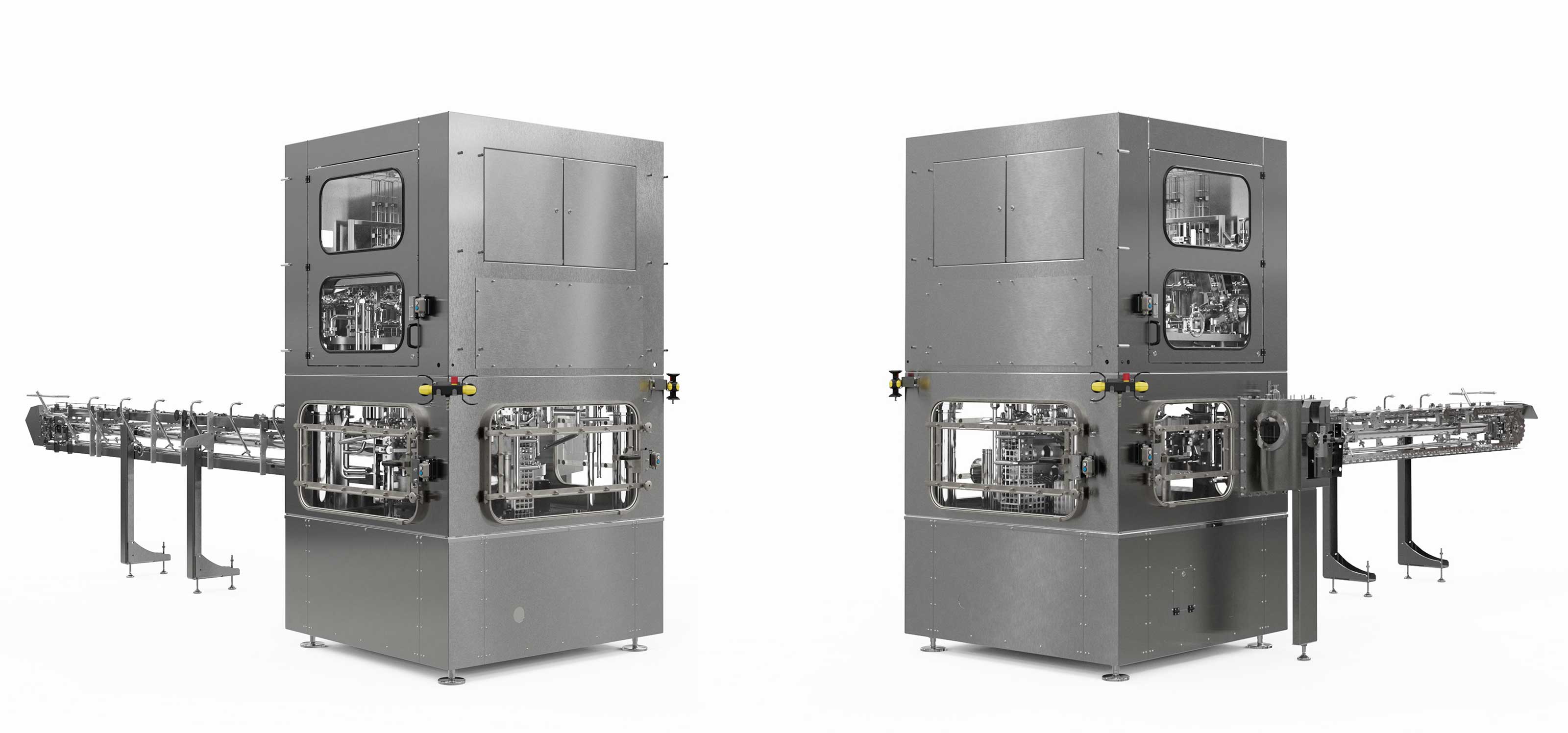
Changing over the discharge starwheel
Maintenance of the control drum
- Swinging out of the quick-set cam for the second operation
- Maintenance
Access to the electrical components
Setting up seaming chucks
Setting up of lid feeds, gassing starwheel, guide parts
- Adjustment of lid feed
- Inspection of the lid magazine
- Adjustment at the quick-set seaming cam (steel/aluminium)
- Maintenance
Adjustment of guidance parts for a change-over at the infeed table
Version in hygienic design
Best hygiene conditions
- Inclined table top for optimum cleaning
- All components in the process area are made of stainless steel
- Process area separated from drive and supply area
- Easy access for change-over and maintenance
- Cleaning through integrated nozzle system
Operator convenience
- Simple change-over to another container
- Automatic height adjustment system
- Good accessibility from three sides as the media and power supply are not provided outside on the can seamer but inside the control cabinet and valve manifold, and/or on the seamer top
Benefits to you
Central media supply
All media are centrally connected via the filler valve manifold; also the internal control and distribution of the media is part of the filler-seamer block. This means that no separate interfaces are required on the can seamer.
Hygienic design
Hygiene plays a central role: The entire seamer area including components is separated from the drive area. Cables and supply hoses are located outside the process area, and all components in the process area itself are made of stainless steel. An inclined table top ensures that the media can drain off in a targeted manner, and foam cleaning of all gas channels is also possible.
Good accessibility
The open design of the seamer allows excellent accessibility during type change-overs or in case of maintenance.
Quick change-over
Numerous features ensure that the change-over to new sizes or types is quick and requires little manual intervention:
- The change-over from steel to aluminium cans is possible in only a short time thanks to the quickly adjustable quick-set seaming cam: The settings are reproducible and the change can be made in less than five minutes.
- Thanks to an automatic height adjustment system, changing to other container sizes requires only a few simple steps. Full parameter management and height adjustment of the entire block is done via the filler's HMI, including, for example, the position of the bubble breaker.
- Thanks to the quick adjustment system of the guide rails on the transfer chain, no manual adjustment work is necessary here either.