Die Welt der Getränke wird immer kurzlebiger: Neue Produkte kommen und gehen irgendwann wieder; manche floppen sofort, manche aber bleiben – und wachsen so schnell, dass die Hersteller oder Markeninhaber gar nicht wissen, wie sie die Nachfrage bedienen können. Ein Beispiel für letzteren Fall ist Hard Seltzer (zu Deutsch „hartes Sprudelwasser“, also Wasser versetzt mit Kohlensäure, Gärungsalkohol und Fruchtgeschmack), das speziell in den USA binnen kürzester Zeit zu einem Milliardenmarkt geworden ist. Von den einst so populären Alcopops spricht dagegen heute kaum noch jemand. Doch wer weiß um die Trends am Markt und wer stellt sich so schnell auf neueste Technologie um? Hier kommen Co-Manufacturer und Co-Packer wie Konings Drinks ins Spiel.
In der Getränkeindustrie wächst die Nachfrage nach Lohnabfüllungen – und davon profitiert Konings Drinks. Das belgische Unternehmen hat deshalb nun erneut eine Komplettlinie von Krones installiert: diesmal eine Dosen-Abfüllanlage an seinem Standort im niederländischen Breda. Dank des Einsatzes von Autoklaven können hier erstmals auch sterilisierte sensible Produkte wie pflanzenbasierte Getränke im Hochleistungsbetrieb abgefüllt werden.
Was macht Konings Drinks?
Das belgische Privatunternehmen produziert und füllt Säfte, Softdrinks, sensible Getränke, Cider, Bier, Wein und Spirituosen für andere Getränkeunternehmen. Dabei stellt es Getränke nach Rezepturen seiner Kunden her und bietet bedarfsgerechte Abfüll- und Verpackungslösungen jeglicher Art, sowohl Glas- und PET-Behälter als auch Dosen und Kartonverpackungen. Konings unterstützt seine Kunden außerdem bei der Produktentwicklung und bringt neue Produkte zur Marktreife.
Es beschäftigt dafür rund 760 Mitarbeiterinnen und Mitarbeiter in sechs Betriebsstätten. Drei Werke befinden sich in Belgien (Zonhoven und Borgloon), je ein weiteres in den Niederlanden (Breda), im Vereinigten Königreich (Boxford) und in Frankreich (Beaucaire). Konings betreibt zudem eigene Fruchtpressen für Äpfel und Birnen mit einer Kapazität von 100.000 Tonnen pro Jahr für die Cider- und Saft-Produktion.
Das Geschäft von Konings wächst stark, in den letzten Jahren immer deutlich zweistellig. Derzeit füllt der Co-Packer rund eine Milliarde Einheiten. Ziel ist es, mit bestehenden und neuen Kunden die Produktion in den nächsten fünf Jahren sogar noch zu verdoppeln.
Drei Abfüllanlagen im Werk
Die Betriebsstätte im niederländischen Breda hat Konings erst im Jahr 2015 von einem großen Fruchtsaft- und Marmeladenhersteller übernommen und anschließend modernisiert. Heute laufen dort drei Abfüllanlagen:
- Eine Linie für Getränkekarton-Verpackungen mit einer Leistung von 8.000 Packungen pro Stunde
- Eine Linie mit dem Trocken-Aseptik-Block PET-AseptBloc D von Krones mit einer Leistung von 20.000 Behältern pro Stunde, die Konings 2016 in Betrieb genommen hatte
- Die neue Dosenlinie von Krones für 60.000 Dosen pro Stunde, die im Mai 2021 ihren Betrieb aufnahm
Über alle Werke verteilt war dies seit 2015 der 16. Auftrag von Konings an Krones, darunter sechs Komplettlinien. Neben der Anlage in Breda hat Konings eine nahezu identische Dosenlinie in Zonhoven, Belgien, installiert, die hauptsächlich CSD und Bier füllt.
Erfahrung mit dem Abfüllen von sensiblen Getränken
Bis zur Inbetriebnahme der Dosenlinie war das Werk auf die Abfüllung von Vitaminwasser, Säften und Smoothies in Kartonverpackungen und PET-Behälter spezialisiert. Dann fiel die strategische Entscheidung, eine vorhandene, ältere PET-Abfüllanlage, die nicht mehr optimal ausgelastet war, auszutauschen und durch die Krones Dosenlinie zu ersetzen. Dafür gab es mehrere Gründe. „Zum einen wächst die Nachfrage nach Dosen stark, zum anderen war bei uns der Platz für eine neue Anlage vorhanden“, erklärt Werksleiter Jan Van Reeth. „Am wichtigsten aber war, dass wir dank der Aseptik-Linie hier bereits Erfahrung mit dem Abfüllen von sensiblen Getränken hatten. Denn wir planen, auf der Dosenlinie kalte Kaffeegetränke, pflanzenbasierte Getränke wie Haferdrinks oder generell pH-neutrale Getränke mit einem pH-Wert von 7,0 abzufüllen. Dafür haben wir auch in drei Autoklaven investiert, mit denen wir solche sensiblen Getränke sterilisieren können. Das Besondere daran ist, dass wir dieses Sterilisationsverfahren im Hochleistungsbetrieb von 60.000 Dosen pro Stunde anwenden können“, erläutert er.
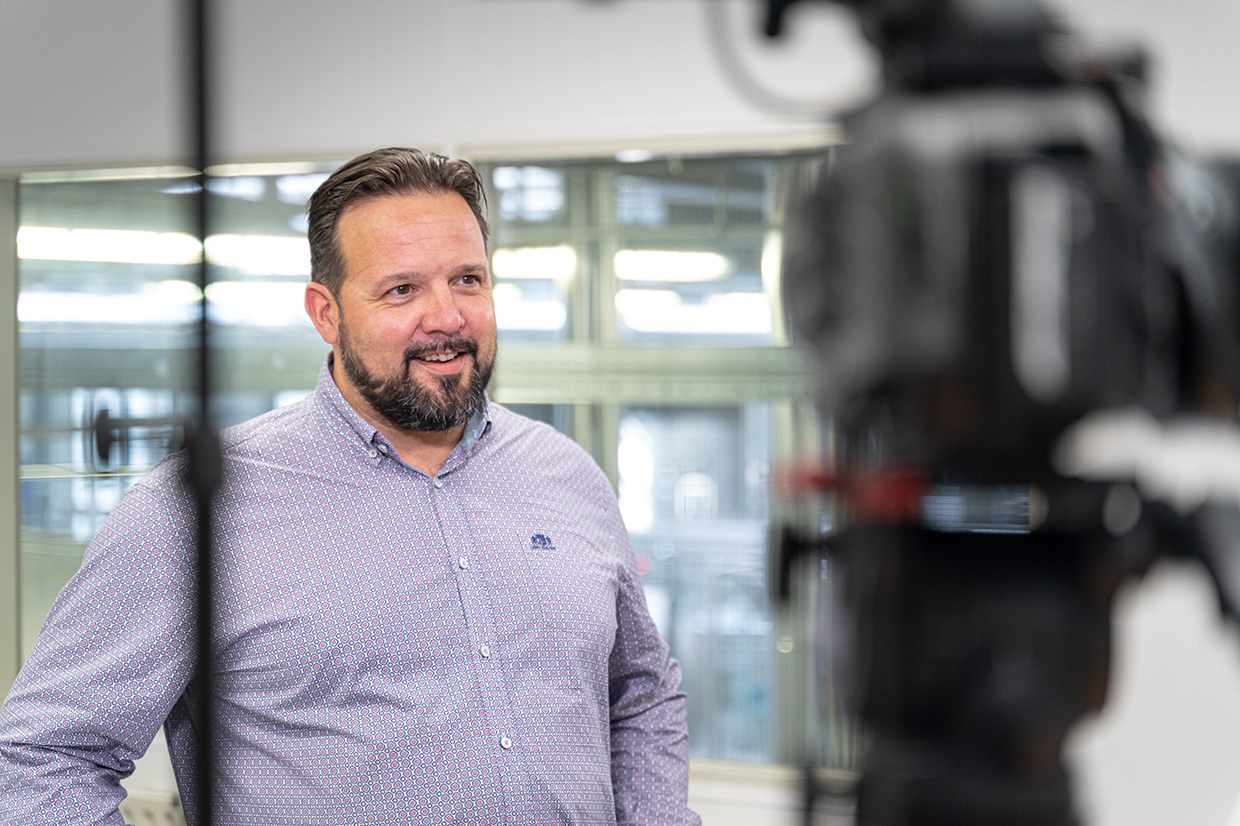
Alles andere als eine Standard-Linie
Die Linie ist eingerichtet für Slim-, Sleek- und Standard-Dosen in verschiedenen Größen (250, 330 und 500 Milliliter). Die Anlieferung der Leerdosen erfolgt just-in-time für die jeweilige Abfüllung, entweder bestellt Konings die Dosen selbst oder der Kunde liefert sie. In der Leergut-Halle steht auch der Behälterabschieber Pressant Universal 1A mit hohem Auslauf. Die Dosen laufen anschließend auf Transportbändern (mit Edelstahldächern als Staubschutz) in die Abfüllhalle. Noch auf der erhöhten Ebene kontrolliert ein Inspektor Cantronic die Dosen, sodass diese auch wirklich leer und zudem nicht verformt sind. In einer Vakuumbrücke erfolgt dann die Codierung mittels Inkjet, die zur Sicherheit doppelt ausgeführt ist.
Nun werden die Dosen in einem Schrägrinser mit ionisierter Druckluft beaufschlagt, auf den Kopf gestellt, und nach unten transportiert. Dort sind sie – wieder richtig herumgedreht – bereit zum Abfüllen.
Nun wird das Produkt, nachdem es von einem Mixer Contiflow ausgemischt worden ist, abgefüllt. Zusätzlich hat Konings vor dem Füller noch ein Edelstahlsieb in die Produktleitung einbauen lassen. Dieses wird nach jeder Abfüllcharge manuell überprüft, ob sich etwaige Rückstände darin befinden. Zum Abfüllen nutzt Konings einen Modulfill VFS-C mit 130 Ventilen. Besonderheit ist, dass dieser auch Widgets für stickstoffhaltige Getränke wie eben Kaffeedrinks in die Dose vorlegen kann. „Damit das Widget später funktioniert, muss der Sauerstoff-Gehalt im Kopfraum sehr niedrig sein“, erläutert Qualitätsmanager Dennis Wols. „Das erreichen wir, indem wir die gefüllten Dosen mit Stickstoff unter dem Deckel beaufschlagen und diesen sofort verschließen.“
Ein Kontrollgerät Checkmat FM-X prüft dann die Füllhöhe mittels Röntgenstrahlung, bevor ein Twister die Dosen erneut auf den Kopf stellt.
Pasteurisieren, sterilisieren oder im Bypass vorbei
Danach bietet die neue Linie drei Möglichkeiten, ob und wie das Produkt weiter behandelt wird. Welche Option angesteuert wird, ist abhängig vom jeweiligen Getränk:
- Die Produkte werden pasteurisiert und die Dosen durchlaufen dazu den Pasteur LinaFlex (wie zum Beispiel Bio-Limonaden).
- Sie werden in den Autoklaven bei bis zu 140 Grad Celsius mit Hochdruck sterilisiert (wie zum Beispiel Kaffeedrinks).
- Die Dosen laufen im Bypass um Pasteur und die Sterilisationseinheit herum (wie zum Beispiel Cola-Getränke).
Die Autoklaven waren dabei ebenfalls im Leistungsumfang von Krones enthalten. Nach einer Pufferstrecke prüft erneut ein Kontrollgerät Checkmat F-X, ob eine Unterfüllung vorliegt. Ein Twister dreht die Dosen wieder auf den Boden und sie durchlaufen einen Trockner Linadry.
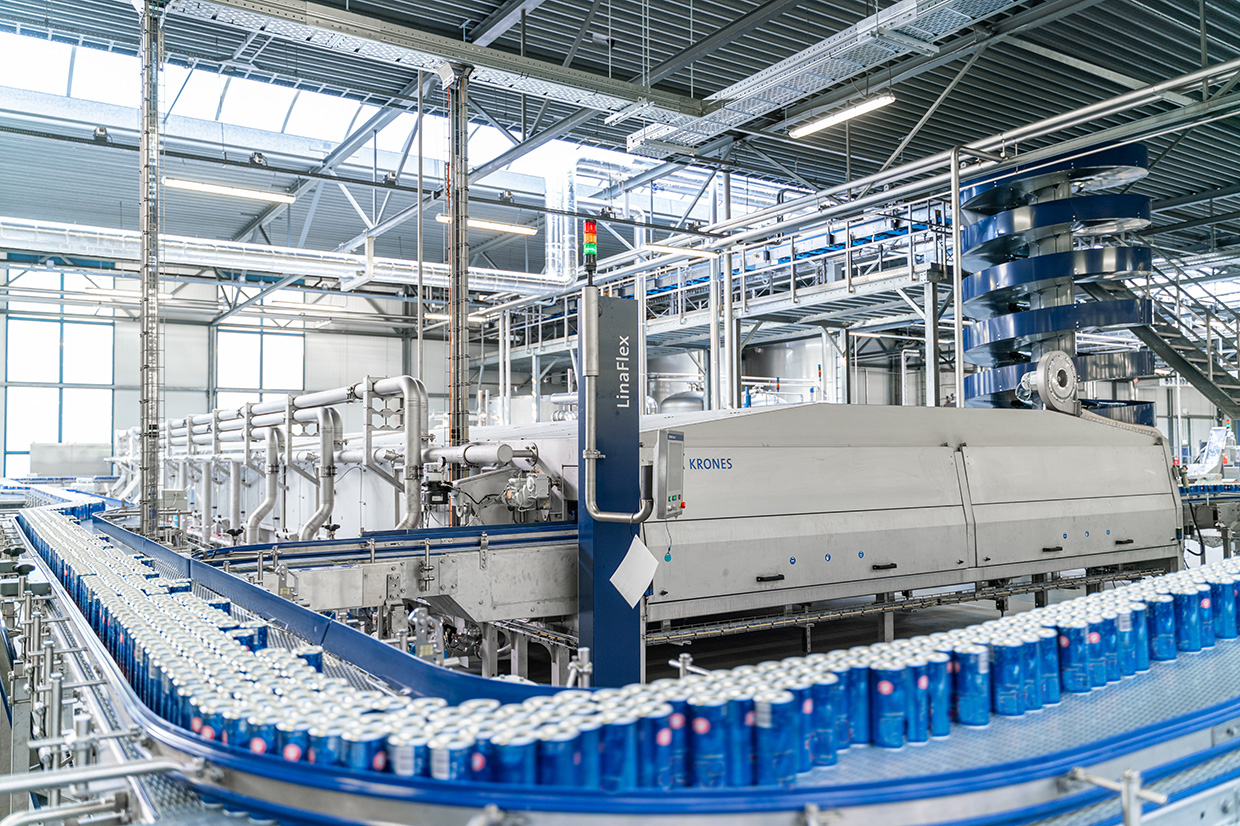
Nun ist die Dose bereit für die Endverpackung. Dazu hat Konings eine Verpackungsmaschine Variopac Pro TFS installiert, die Trays mit Folie herstellt. Die Anlage ist dabei auch für die zukünftige Nutzung von Recycling-Folie ausgelegt. Formatwechsel geschehen halbautomatisch, die Parameter müssen manuell eingegeben werden. Diese Anlagen im Trockenteil gehören auch zu den ersten, die Krones im Bereich der Automatisierung bereits von Siemens S7 auf Siemens TIA Portal umgestellt hat.
Ein Schnecken-Vertikalförderer bringt die fertigen Packungen dann auf ein höheres Niveau, sodass sie über eine Brücke eine Straße überqueren können und schließlich in die Vollgut-Halle gelangen. Hier befindet sich der Palettierbereich mit einem Gruppiersystem Robobox T-GS sowie einem Palettierer Pressant PalBloc 1AJ. Um den Prozess zu komplettieren, lieferte Krones auch die CIP-Anlage VarioClean.
Extrem kurze Installationszeit
„Wir haben gemeinsam mit Krones die Dosenlinie binnen extrem kurzer Zeit installieren können: Von Auftragsvergabe bis zur ersten Dose vergingen nur sieben Monate. Das musste so schnell gehen, da einige Kunden mit pflanzenbasierten Getränken schon in den Startlöchern standen“, sagt Group Project Manager Stijn Van Paemelen, der schon die PET-AseptBloc Anlage mit aufgebaut hatte und jetzt das zentrale Engineering von Konings leitet. „Das hat trotz Covid-Maßnahmen super funktioniert, es kamen etwa 100 Lkws mit Material hier an, außerdem waren bis zu 50 Monteure von Krones vor Ort. Das war sehr gut organisiert, alles lief wie eine gut geölte Maschine“, lobt er.
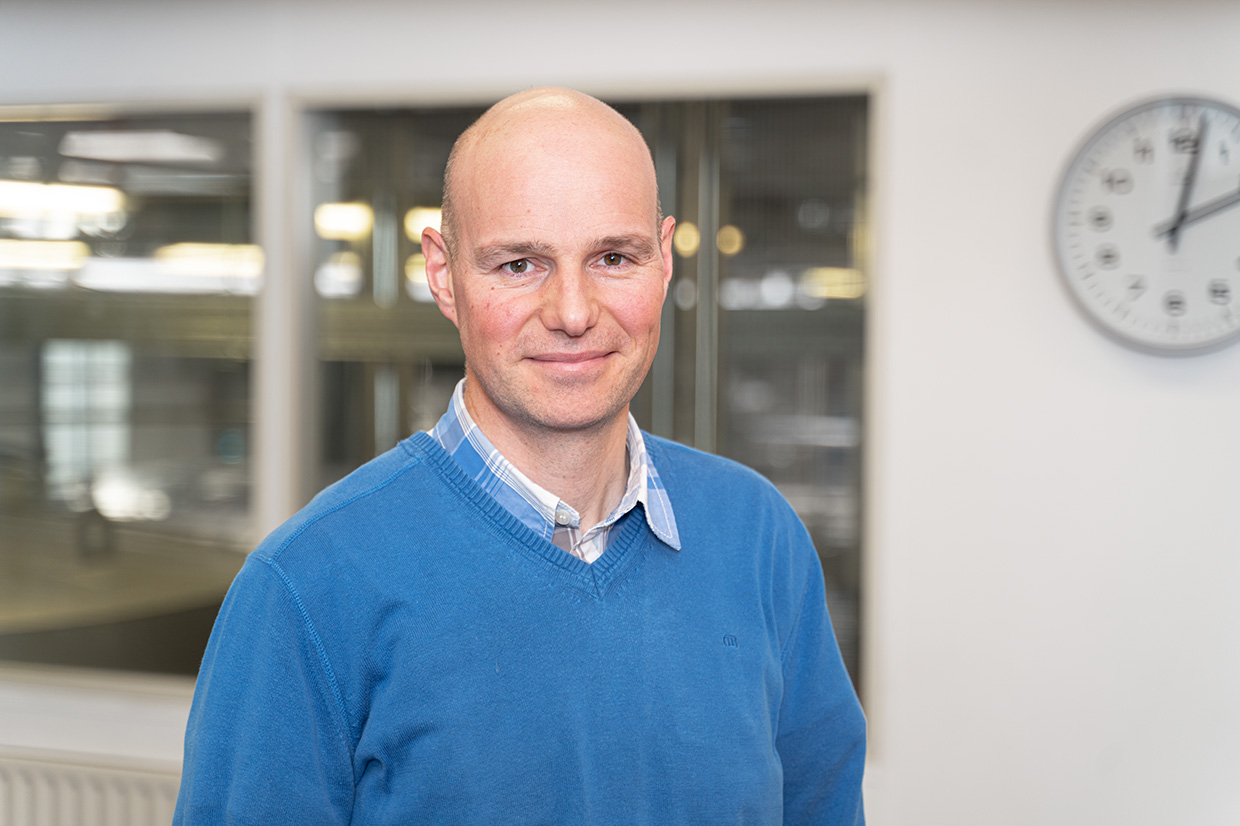
Doch obwohl die neue Linie schon läuft, ist die Arbeit für Krones längst nicht beendet: Noch ausstehend ist die Aufgabe, das Monitoring-System SitePilot Line Diagnostics zu implementieren. „Wir müssen als Co-Packer sehr flexibel mit der Linie arbeiten können. Deshalb haben wir auch eine 60.000er und keine 120.000er Dosenlinie gewählt – und um diese möglichst effizient zu betreiben, brauchen wir das Linien-Management-System“, betont Stijn Van Paemelen.
Ziel ist es, bei Umstellvorgängen drei verschiedene Produkte gleichzeitig auf der Linie verarbeiten zu können: Während Produkt 1 auf Paletten gestapelt wird, ist Produkt 2 noch im Füller und von Produkt 3 werden gerade die Leerdosen abgeschoben. Denn Konings verarbeitet Chargen verschiedener Größen: von nur rund 80.000 Einheiten bis hin zu mehreren Millionen Dosen. Derzeit läuft die Linie im Zweischichtbetrieb, etwa drei bis zehn Mal pro Woche ist eine Umstellung erforderlich.
Ebenso wichtig wie die Flexibilität ist für Stijn Van Paemelen die Nachverfolgbarkeit. Auch diese Anforderung erfüllt die neue Linie dank der komplett automatischen Codierung von Primär- und Sekundärverpackung.
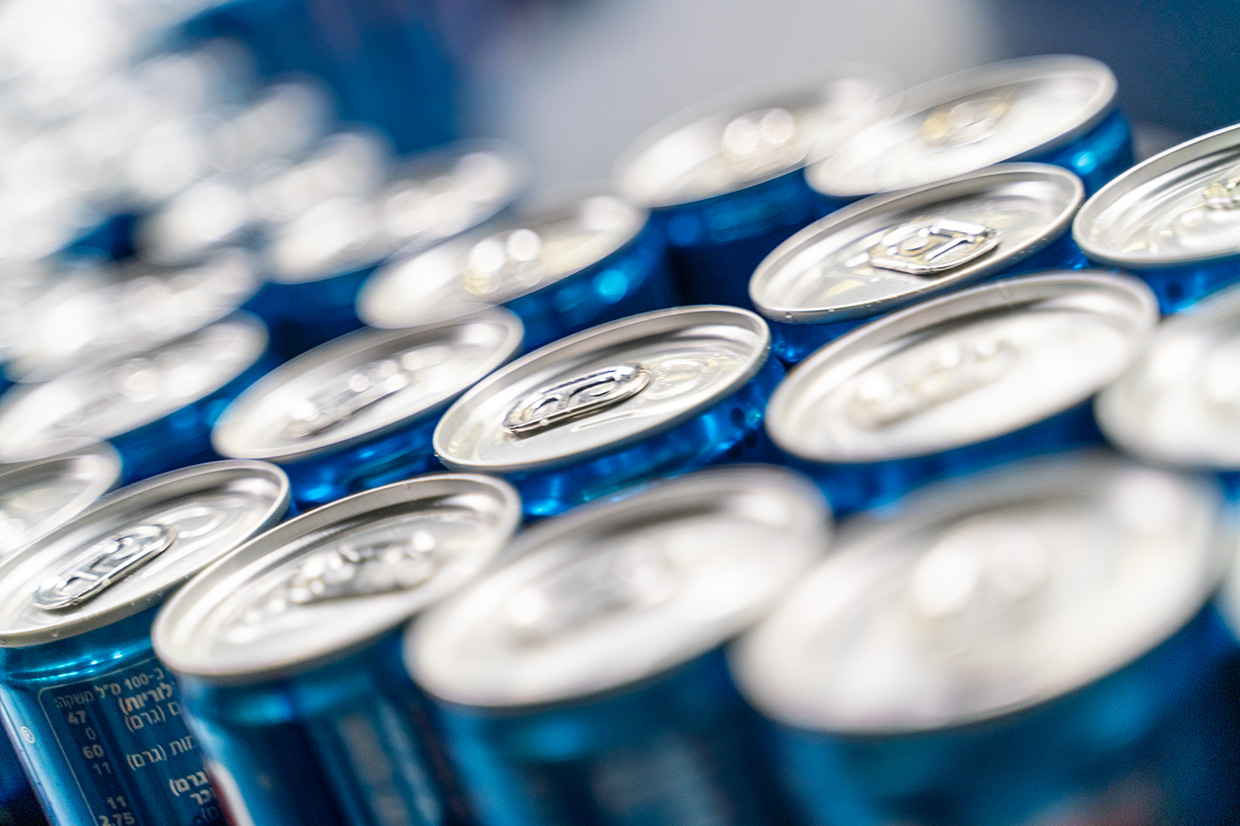
Kräftig in die Abfülltechnologie von Kaffeedrinks investiert
„Als Markeninhaber kann man nicht ständig in neue Abfüllanlagen investieren, weil ja immer auch die Overhead-Kosten eines Werks zu berücksichtigen sind. Deshalb gibt man den Auftrag zur Abfüllung lieber an professionelle Co-Manufacturer wie Konings“, sagt Werksleiter Jan Van Reeth. „Unser großer Vorteil ist dabei die Flexibilität, die wir unseren Kunden bieten können, wenn sie zusätzlich zu ihrem bestehenden Portfolio mal etwas Neues ausprobieren möchten. Außerdem besitzen wir ein großes Know-how im Umgang mit sauerstoffempfindlichen Getränken“, erklärt er. „Wir haben jetzt kräftig in die Abfülltechnologie von Kaffeedrinks investiert und hoffen, dass dieser Markt wächst. Wir profitieren dabei davon, dass wir Produkte verschiedener Kunden verarbeiten, denn für eine einzelne Marke aus diesem Segment wäre die Investition in diese neu geschaffenen Kapazitäten zu riskant“, ist er überzeugt.